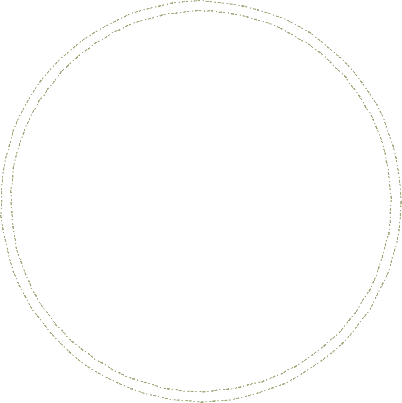
作業員の製造工程への入退室基準を設け、製造工程内に異物を持ち込まないようにしています。
工場の清掃メンテナンスが適正に行われているか確認するために、各工程のクリーンチェックを毎月行います。製品がより清潔な環境で製造されるよう、清掃の確認、道具などの管理状態を確認します。客観的に状況を確認するために、部外のメンバーも参加します。
作業室内の空気圧を廊下より高くすることで、室内にほこりやちり等が入らないように管理しています。
クリーンルームには、へパフィルターと呼ばれる特殊なフィルターを設置し、作業室内の空気を常に清潔に保っています。へパフィルターは、0.3ミクロン以上の微粒子を99.97%以上除去できるフィルターです。
工場はクリーンゾーンや一般ゾーン、丸剤工場や錠剤工場などでゾーンが区分けされています。ゾーンごとに使用目的が異なるため、多数の人が出入りすることは好ましくありません。出入りするスタッフを制限するため、ゾーンごとに作業着の色分けを行い、担当外のゾーンに入ってしまった場合はすぐに発見できるようにしています。
一般作業用
エキス剤製造用
丸剤製造用
錠剤製造用
SOPとは作業の手順を記したものです。
日野製薬ではSOP通りに作業が行われるよう、すべての作業ごとにチェック項目を設け、完了したら作業者がサインをします。計量作業などの重要な工程では、2名体制で厳しくチェックを行っています。
安心・安全な製品をお客様にお届けするために、原料・資材の入荷から製品の出荷まで何段階にもわたり試験を行っています。
工場で使用する製造用水は、遊離残留塩素・pH・濁度について毎週水質試験を行い、月に一度外部機関の試験結果を確認します。
全ての原料についてメーカーと取決めを交わし、規格に適合する原料のみ先行サンプルを入荷します。サンプルに対して自社で試験を行い、適合を確認したうえで、実際の原料入荷となります。万が一先行サンプルで規格に適合しなかった場合は、別ロットを再度発注します。
衛生管理基準書を整備し、製薬会社として高い衛生意識を持って衛生管理を行っています。細かなところでは、社内で使用する石鹸・消毒液なども使用期限を規定し徹底して管理しています。
クリーンルームは、常に清潔な状態が保たれるよう、浮遊粒子数測定、落下菌測定、各工程の衛生チェック等を行っています。
空調にはヘパフィルターという特殊なフィルターを採用し定期的に性能の点検を行います。
原料倉庫・工場・製品倉庫など、製品に影響を及ぼす恐れのある場所は、温湿度記録を取り毎日チェックしています。改善が必要と判断された場合には適切な処置を施します。
工場・倉庫等で毎月モニタリングを行い、虫などの混入対策を行っています。
ハード面の対策だけではなく、ソフト面の対策もしっかり行っています。毎月定期的に製造作業や品質管理などに関して教育訓練を行い、製造に関わるメンバーの意識と知識向上を促しています。
社員全員にカードキーを配布し、入退室管理を行っています。特に、工場及び品質管理部門への入室はメンバーを限定し、関係者しか入れないようにしています。